一、LTCC基板电路概述
低温共烧陶瓷 (LTCC) 技术是集互联、无元件和封装于一体的多层陶瓷制造技术。随着科技的不断进步,现在的电子产品的外观可以变得更小更薄,但功能更强大。以手机的无线通信行业为例,手机的尺寸缩小,早期的移动电话的功能是从最简单的音频传输数据开始,现在已经发展成掌上网络电脑。如果可以将部分无源元件集成到基板中,则不仅有利于系统的小型化,增加电路的组装密度,还有利于提高系统的可靠性。目前的集成封装技术主要包括薄膜技术、硅片半导体技术、多层电路板技术和LTCC技术。 LTCC技术是一种低成本封装的解决方案,具有研制周期短的特点。低温共烧陶瓷技术可以满足后者轻、薄、短、小的需求。但是低温共烧陶瓷基板具有高硬度、易碎的特性。因此,切割机切割硬基材时,基材与切割刀片之间会产生较大的摩擦力,摩擦产生的应力会传递到切割刀片上。
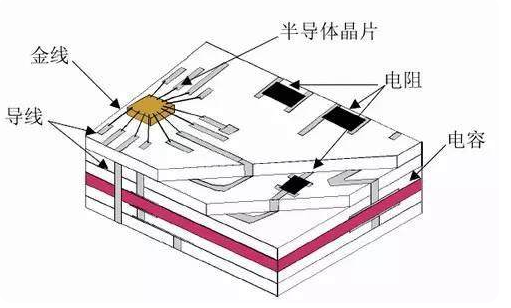
2、LTCC基板加工技术
图2为LTCC基板制造工艺流程图,主要包括混料、流延、打孔、填孔、丝网印刷、层压、等静压、排胶烧结等,下面简要介绍各工艺的主要工序。
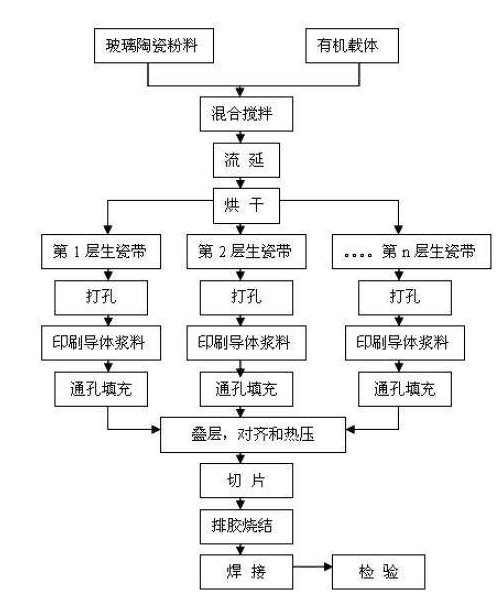
混料和流延:将有机物(主要由聚合物粘合剂和溶解于溶液的增塑剂组成)和无机物(由陶瓷和玻璃组成)按一定比例混合,采用球磨法研磨均质,然后浇注在一个移动的载带上(通常为聚酯薄膜),通过一个干燥区,除去所有溶剂,通过控制刀片间隙,流延成所需厚度。此工艺的一般厚度公差为±6%。
冲孔:采用机械冲孔、钻孔或激光钻孔技术形成通孔。通孔是在生瓷片上冲出的小孔(通常直径为0.1-0.2mm),用于不同层间互连电路。在这个阶段还要冲模孔,以帮助叠片时对准;对准孔用于印刷导体和介质时自动对位。
印刷:使用标准厚膜印刷技术对导体浆料进行印刷和烘干。通孔填充和导体图形在箱式或链式炉中根据相关工艺温度和时间干进行烘干。根据需要,所有电阻器、电容器和电感器都在此阶段进行印刷和烘干。
通孔填充:采用传统的厚膜丝网印刷或模板挤压把特制的高固体颗粒含量的导体浆填充通孔。
排胶和烧结:200-500°C之间的区域称为有机排胶区(建议在该区域叠层保温至少60分钟)。然后在 5-15 分钟将叠层共烧至峰值温度(通常为 850°C)。烧成金属化的典型排胶和烧成曲线需要的2-10h。烧成的部件准备好后进行烧制工艺,例如在顶面上印刷导体和精密电阻器,然后在空气中烧成。如果 Cu用于金属化,则必须在 N2 链式炉中进行烧结。
检验:然后对线路进行激光调阻(如果需要)、测试、切片和检验、LTCC 封装中可用钎焊引线或散热片(如果需要)。
3、LTCC基板电路加工案例
3.1 LTCC基板微通孔形成技术
微通孔的形成是低温共烧陶瓷多层基板高密度互连中极为关键的工艺,因为孔径大小和位置精度都将直接影响布线密度和基板质量。为了实现超高密度,通孔孔径应小于100μm。 LTCC生瓷带的微孔制作方法有:机械冲孔和激光打孔。
3.1.1 机械冲孔
用数控冲床冲孔是对生瓷带冲孔的较好方法,尤其是定型产品,冲孔更有优势。用冲床模具一次可冲出上千个孔,最小直径可达50μm。冲孔速度快,精度高,适合大批量生产。在生陶瓷带上制作微通孔时,需要一个与微通孔尺寸相同的冲头和一个模具。模具的开口一般比冲头模直径大12.5μm。
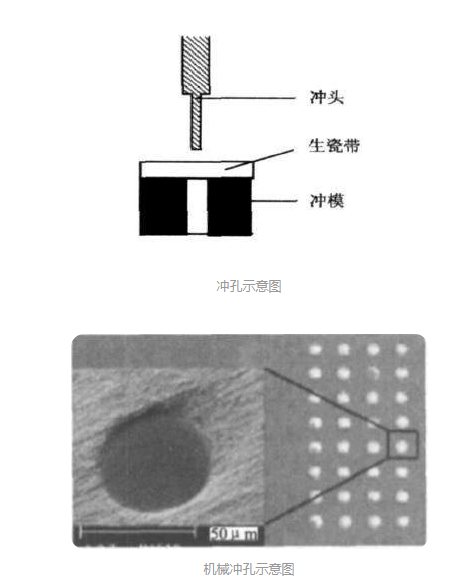
制作微通孔的关键技术点是:安装和操作微小冲头。当冲头的直径小于100μm后,由于坚固度的降低,冲头的安装和操作会越来越困难。大多数冲压缺陷不是在冲压过程中形成的,而是由于操作不当造成的。因此需要专用工具来安装微型冲头,并且在安装和操作过程中必须避免冲头的撞击和损坏。对准冲头和冲模。要使机械冲孔生产出高质量的通孔,很大程度上取决于冲头和模具之间的对准度。如果两个装置没有对准,通孔质量会下降,冲模会受损,冲头也可能会断裂。确保微通孔制作质量,微通孔的质量包括微通孔的形状、尺寸和内部贯穿状况。
机械冲孔形成的微通孔的直径和间距较好。顶部边缘比较平滑,但底部边缘比较粗糙,内壁比较平直。顶部和底部开口大小相连近。不同厚度的LTCC陶瓷带所生产的微通孔尺寸也是一致的,即陶瓷带的厚度与通孔尺寸的比率不会影响通孔的质量。使用机械冲孔的方法,在厚度为50-254 μm的不同LTCC瓷带上形成的50、75和100 μm的微通孔表明,不同尺寸的微通孔在LTCC瓷带正面和背面的开口直径大小都在允许的测量误差范围内,但在陶瓷带背面的通孔开口偏差更大。显微镜下检查冲孔后模开口的变化,比原来的开口尺寸有所增加,这是冲模开口磨损造成的。不同微通孔的分析数据表明,冲头的尺寸决定了通孔正面开口的大小,而背面通孔的直径则受冲模开口大小的影响。
因此,当冲模开口因磨损超过一定值时,微过孔背面的开口会大大增加,此时应更换冲模。另一个影响微过孔质量的因素是过孔中的残留物,它是残留在通孔开口处的一小片LTCC陶瓷带,在冲孔时没有完全去除。这些残留物主要在LTCC生瓷带层的背面,与通孔边缘相连,一般为10-25μm。含有残留物的通孔数量随着通孔尺寸的增大而减少,残留物的含量与陶瓷带的厚度无关。
3.2微孔注入法
通常微孔注入法效果最好,但需要专门的设备。在微孔注射系统中,影响通孔填充质量的主要因素包括注入压力、注入时间、填充浆料粘度以及LTCC陶瓷带与通孔填充掩模之间的对准情况。一旦确定了适用于整个制造工艺的参数,就可以在几秒钟内在 LTCC 生瓷带层中填充数千个通孔。注意微孔金属化的未填充、过填充和少填充。
填充了银浆的 75μm 微通孔。填满浆料的通孔具有所需的尺寸和满意的填充质量。 LTCC 瓷带背面过度填充的缺陷,这是由于在真空卡盘和 LTCC 瓷带之间使用了不合适的多孔衬纸造成的。当填充通孔时,掩模版与LTCC陶瓷带之间存在未对准状况时,与掩模版接触的LTCC生瓷带通孔的正面会出现过填充缺陷。间距为 75μm 的顶部通孔。由于过度填充而使孔距被缩短。如果通孔之间发生过填,则必须增加孔间距,以避免过填充的额外浆料导致短路,但这会降低内部互连密度。
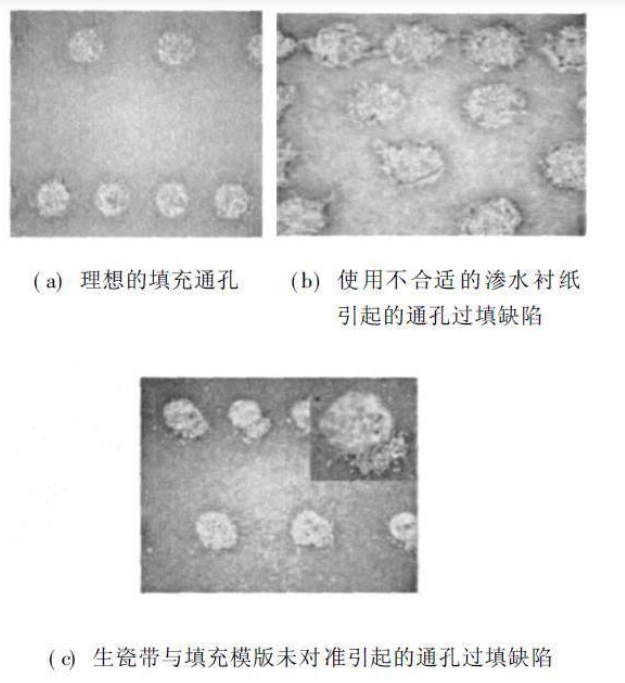
3.3 LTCC基材排胶和烧结
烧结的技术要点是控制烧结收缩率和基材的整体变化,控制两种材料的烧结收缩性能,避免产生微观和宏观缺陷,以及实现导体材料的抗氧化作用和在除烧结过程中去除粘合剂。普通LTCC基板的烧结收缩率主要是通过控制粉体的粒径、流延粘结剂的配比、热压叠片的压力、烧结曲线等手段来实现的。但是一般LTCC共烧体系沿X-Y方向的收缩仍然在12-16%。借助无压烧结或压力辅助烧结等技术,可以获得X-Y方向零收缩的材料。
实现零收缩的工艺有: 自约束烧结,基材在自由共烧过程中表现出自身抑制平面方向收缩的特性,这种方法不需要增加新设备,但材料体系独特,不能满足制造不同性能产品的要求。压力辅助烧结,通过在Z轴方向加压烧结来抑制X-Y平面上的收缩;无压力辅助烧结,在层压材料之间加入夹层(如在LTCC烧结温度下不烧结的氧化铝),以限制X和Y轴方向的移动,烧成后研磨掉上下面夹持用的氧化铝层;复合板共同压烧法,将生坯体粘附在金属板(如高机械强度的钼或钨等)进行烧结,利用金属片的束缚作用降低生坯体在X-Y方向的收缩。陶瓷薄板和生坯片叠层共同烧结法,陶瓷薄板作为基板的一部分,烧成后不必去除,也不存在抑制残留的隐忧。
3.4 LTCC电路板大面积接地钎焊
LTCC电路基板大面积接地钎焊工艺设计,提高LTCC电路基板大面积接地钎焊的钎着率和可靠性的钎焊工艺。在LTCC电路基板接地面设置 (Ni+M)复合金属膜层,根据试验测试对比,其耐焊性(>600s)明显优于常规金属化接地层(常规要求>50s);在LTCC电路基板的接地面一端预置一个“凸点”,通过X射线扫描图的对比分析,增加“凸点”的设计提高了大面积接地钎焊的钎着率。研究表明:新的钎焊工艺设计保证了LTCC电路基板大面积接地的钎焊可靠性和一致性。
3.4.1 试验材料和设备
LTCC电路板:采用Ferro A6-S生陶瓷烧结而成的多层电路板,尺寸80mm x 30mm x 1.2mm,组件壳体材料为Kovar合金,盒体壁厚1.0mm,底部尺寸80mm x 30mm,底部厚度为2.0mm,焊料为0.1mm厚的Sn63Pb37焊片。
测试设备:自制的充氮气手套箱,内有加热台,加热台的额定工作温度为450℃。
X射线检测设备:MACROSCIENCE MXR-160。
数码相机设备:OLYMPUS MODEL NO. C5060。
3.4.2 LTCC电路板表面金属化方法
LTCC电路基板表面金属化的方法目前大致有两种:厚膜烧结法和溅射薄膜电镀增厚法。溅射薄膜再电镀增厚法虽然在单层陶瓷基板的薄膜电路加工中得到了广泛的应用。但是在LTCC电路板仍处于探索阶段。目前提高LTCC电路板耐焊性的一般方法是烧结一层钯银。
3.4.3 耐焊性测试方法
选择三种试样进行耐焊性测试对比:(1)厚膜钯银层(约12μm)试样; (2) 厚膜金层(约37μm)试样; (3) 设置含Ni Barrier layer 3(Nj+M)复合金属膜(约10μm)样品,M为金属代号。
参考GJB548A-96(微电子器件试验方法和程序):将基板垂直浸入(215±5)℃熔融焊料的锡槽中,每次58,共10次(焊料成分为63Sn37Pb的共晶焊料,焊剂为25%的松香酒精溶液)清洗、涂焊剂,被检图形应无翘曲、脱落、断裂、被熔蚀不超过20%的面积。以上3种试样均能通过耐焊性的试验检测标准,且未见被熔蚀的地方,随后将上述3种试样(新的试样)金属化层表面上放置涂有焊剂的焊片,在氮气保护下,在240℃(设定值)的热台上加热保持,观察焊料相应试样金属化层表面的熔蚀情况。
3.4.4 LTCC电路板与盒体的气保焊方法
可实现LTCC电路基板与箱体底部大面积钎焊的方法有:气体保护钎焊、真空钎焊、空气中热板钎焊。在空气中相应的软钎焊料呈液态时更容易与空气中的氧气发生化学反应,因此气体保护钎焊与空气中热板钎焊相比具有明显的优势。但是,气体保护钎焊和真空钎焊两种方法各有优缺点。真空中热量的传导主要靠辐射,遮蔽效应较明显。由于微波元件尺寸较小,每个工件上的温度不均匀,导致部分工件温度高,焊锡过度流动,部分工件温度不足。未完全熔化和铺展,钎焊质量一致性差,加热周期长,效率低。
气体保护钎焊热传导的三种方式并存,操作方便,效率高,然而由于气体的存在钎着率受到限制。在一般条件下可达75%以上,呈随机分布。对于微波电路来说,带来了很大的不确定性。为了提高钎焊率,采用了预先设置“凸点”的方法。凸点的材料与大面积钎焊的焊片材料相同。凸点的制作方法,在对应位置放置适量的锡膏,通过热风回流成凸点。凸点的大小随基板的长度而作相应变化。凸点制作完成后,在盒体底部预先设置与已清除氧化皮且与凸点成分相同的焊片。在有气体保护下的热板上加热来实现LTCC与盒体底部的大面积接地焊。
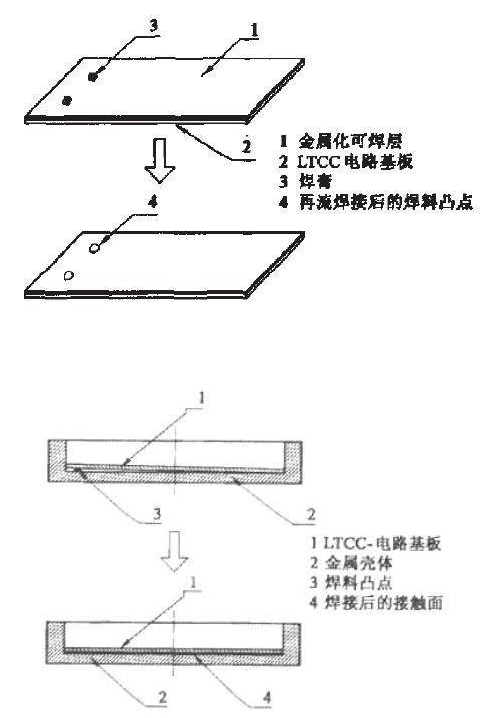
3.4.5 钎焊率检测
大面积钎焊后,理论上焊料利用毛细现象的原理,会尽可能地填充LTCC与箱体底部之间的空隙。但是由于保护气氛的存在,熔化的焊料会随机形成多个包围圈,将气体包裹在里面。钎焊界面内部有空腔或凝固过程中焊料合金松动,则X射线很容易通过,从而在成像图像中产生白色或灰白色的亮点,未设置“凸点”焊接工艺的X射线扫描图,箭头表示明显的焊接缺陷,钎着率在75%左右,设置“凸点”焊接工艺的X射线扫描图,箭头所指为轻微焊接缺陷,钎焊率为98%以上。由于“凸点”的存在,加热过程中人为造成LTCC基板两端的温度存在差异。随着“凸点”的缓缓坍塌,有利于盒体底部焊料与LTCC基板之间夹杂气体排除。 X射线检测图片证明在气体保护下,在基体的焊接面上设计“凸点”可以提高钎焊率。
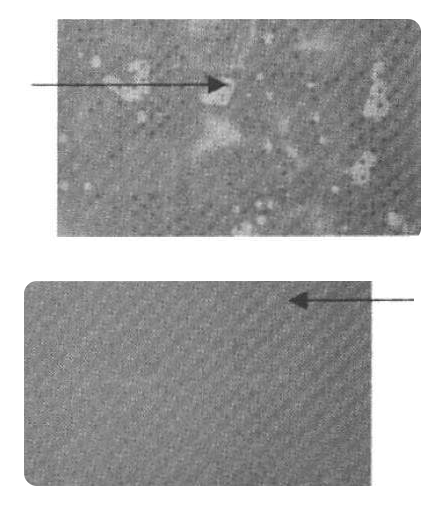
3.4.6 LTCC电路板大面积接地钎焊结论
(1)设置(Ni+M)复合金属膜层,大大提高了LTCC基板大面积金属化层对Sn63Pb37焊料的耐焊性,保证了LTCC基板与盒体的可靠钎焊;
(2)采用气体保护,在LTCC基板的焊接面上设计“凸点”在提高LTCC电路基板与盒体之间的钎焊率非常有效。
3.5 LTCC 电路检测
对排脂、烧结、焊接后的LTCC元件必须进行多方面的检测,以确保其性能的可靠性。 这些检测包括外观、尺寸、强度、电气性能等方面。